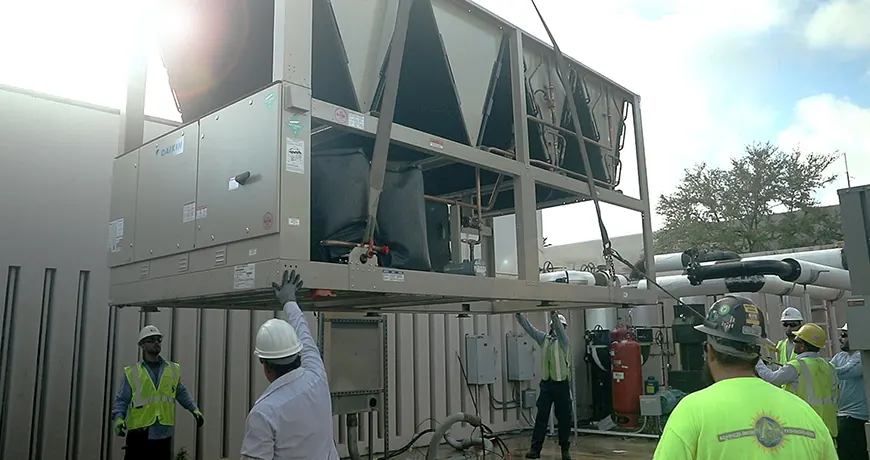
Stirling Elementary School
Stirling Elementary School in Hollywood, Florida, was experiencing issues with cooling efficiency due to an outdated Trane chiller system. The 24-year-old system’s coils were falling apart, causing it to work harder and use more energy while lacking the ability to keep students and staff comfortable. Advanced Air Systems was hired to install an upgraded HVAC system throughout the campus as part of Broward County Public Schools’ SMART Bond Program to improve schools.
Project Scope of Work
Advanced Air System’s 10-person crew replaced the outdated Trane system with a Daiken air-cooled chiller system, providing greater cooling capacity while using less energy. The new 130-ton enhanced system consists of one chiller, seven air handlers installed inside the building, and two condensers installed on the roof curbs for roof-mounted equipment. The old condensers were replaced with modern components to increase efficiency and effectiveness and were swapped out in tandem with the re-roofing, requiring consistent coordination and communication. The new air handlers and pumps were equipped with Variable Frequency Drives (VFD) which match motor Power usage to the load requirements by adjusting power and down to meet the school’s demands.
To remove the old system, the crew made use of a 100-ton crane for temporary relocation of the old system and install the new system.
The Daiken system provides the reliability needed to keep the more than 500 students and faculty comfortable and focused. With an expected lifespan of 20 years, the system comes with a five-year warranty and will be maintained monthly by the school maintenance team, which will check refrigerant levels and components.
Overcoming Challenges
Standard safety procedures and checks were followed throughout the project, resulting in zero safety incidents and ensuring the well-being of students, staff, and crew working in an occupied building.
The project encountered several challenges related to creating a temporary cooling solution. The temporary unit could not require increased power usage since the school lacked the additional power supply necessary to provide a temporary chiller. The crew began to cool the building during installation by disabling all air handlers inside the building. Package units were placed outside of the building and connected through the windows. While piping for the new system was being installed, the chiller had to be turned off, and existing pumps and chiller were placed to the side while hoses were connected for use as a temporary system. The temporary system could not be shut off until the new system was fully operational. The client was happy with this solution, providing efficient cooling during installation.
Another challenge encountered was significant product and installation delays due to the pandemic. The project manager worked with suppliers to adjust the installation schedule as the units became available.
Project Completion
Commencing in June 2020, the project was completed on time, within budget, and with no safety incidents, in August 2022.